Ply girder frame baseboards
Posted
Guest user
Posted

Full Member
If not, then the single skin might be an option. Those Barry Norman "box girders" are very time consuming to make ……..:hmm
'Petermac
Posted

Full Member
Is there any difference between the "Barry Norman" box girder structure and the single panel ply frames Sam ?
If not, then the single skin might be an option. Those Barry Norman "box girders" are very time consuming to make ……..:hmm
Yes, Peter, with the Barry Norman system, you get a free subscription to the BBc's 'Film' programme……..
http://www.youtube.com/watch?v=k4lRmG_UXy8 Remember?
[If it strikes a chord with you, hear the 'chords' here, by a ex-Juliard, classicly trained pianist who could not appear at major U.S. concert venues at the time of her pre-eminence because they did not have dressing rooms for black performers…..shame on all of us for not knowing and speaking out sooner.]
Sorry if this is a bit deep, not a 'trolling' or a wind-up, I promise…
http://www.youtube.com/watch?v=-TarrSrx4v0
Doug
[A long-time Nina Simone fan]
Last edit: by Chubber
'You may share the labours of the great, but you will not share the spoil…' Aesop's Fables
"Beer is proof that God loves us and wants us to be happy" - Benjamin Franklin
In the land of the slap-dash and implausible, mediocrity is king
"Beer is proof that God loves us and wants us to be happy" - Benjamin Franklin
In the land of the slap-dash and implausible, mediocrity is king
Posted

Full Member



Without getting political, I'd agree with everything you say. :cheers
'Petermac
Posted
Guest user
Posted

Full Member
I use a Black & Decker workmate, which enables me to clamp both side pieces and at least two of the spaces all at the same time. The spacers are pre-glued, then slotted between the sides and the workmate tightened.
As the top half of the frame is exposed, I can drill & screw each side of the frame, the move the whole frame along and do the next couple of blocks. Once the upper half is done, the frame is inverted and the lower screws put in.
Keeping the frame in the workmate also helps to keep the whole lot square, too.
Stubby47's Bespoke Model Buildings
All photos I post are ©Stu Hilton, but are free for use by anyone.
Posted

Full Member
What, to me, takes the time, is actually making the girders. Everything is "doubled" - the cutting, the gluing, the stapling into the spacer blocks (in my case) and, it's amazing how much wood I used up just for the spacers……..:shock:
Whilst I'd still have the blocks for the corners and cross member positions to cut out, if I could then just use single strips of ply for the frames, I wouldn't have to cut the spacers for the "box" beams and only half the ply. I would however, have to use diagonal stretchers to hold the whole thing square. I don't use those with the "box" beams………..:roll:
It might be a close run thing but I suspect it would be quicker and probably cheaper although the ply would have to be thicker. For the boxed beams, I only use 4mm ply but would probably have to use 10mm if it wasn't "boxed".
'Petermac
Posted

Full Member
I too only use thin ply (4.5mm) with 1" x 4" x 4" spacers with 8" to 11" gaps between them.
Stubby47's Bespoke Model Buildings
All photos I post are ©Stu Hilton, but are free for use by anyone.
Posted
Guest user
My layout baseboards are 12mm ply built in box form but only single thickness. They have been made for over 5 years now and show no sign of twisting. The box construction is 300mm squares by 100mm deep. This egg box structure is then covered by 12mm thick ply. 50mm x 50mm legs are just bolted to this frame in appropriate places for legs with screw adjustable feet. Each vertical piece has a slot cut into it for the wiring. I have an L shaped layout 2.5Mtrs x 900mm deep and the other leg is 1.6Mtrs long by 700mm deep. They are attached by 12mm bolts and wingnuts together with cabinet makers biscuits for alignment.
Hope this is helpful
Puffer
Posted

Inactive Member
Max
Port Elderley
Port Elderley
Posted

Full Member
This is what I call a "box girder" or "box beam":

I'm suggesting that I might be able to use just a single piece of ply (albeit thicker) and do away with the duplicate cutting of ply "cheeks". What are currently the spacers, would become blocks into which the "rungs" are screwed in a conventional "ladder" type of frame construction.
'Petermac
Posted

Full Member
..there is a lighter, more rigid alternative, if you have a saw blade that will cut a kerf of the correct width to allow the direct insertion of thin ply [as thin as 2mm will still work] then girders made of 1" square softwood either side of a 3 1/2" play strip, end-glued into 4" boards as shown below. The 'I' beam is amazingly rigid, this proportion and construction was used in early home-build aeroplanes!
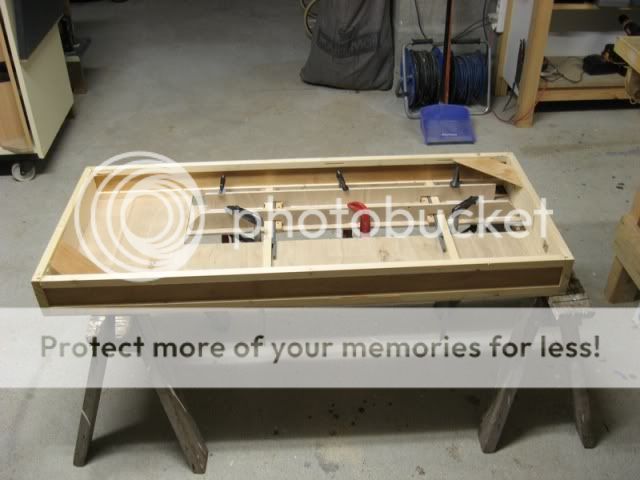

'Evostick Resin W' white glue is quite good enough, no need for Aerolite or P.V.U. types.
Doug
'You may share the labours of the great, but you will not share the spoil…' Aesop's Fables
"Beer is proof that God loves us and wants us to be happy" - Benjamin Franklin
In the land of the slap-dash and implausible, mediocrity is king
"Beer is proof that God loves us and wants us to be happy" - Benjamin Franklin
In the land of the slap-dash and implausible, mediocrity is king
Posted
Guest user
I was reminded today that some of our modules are closer to 20 years old with no problems encountered. We used 6/7mm exterior grade 5 ply. I also have some even older single skin modules 915 x 305 x 100 made from 4mm ply that are still quite sound. I have recently assembled these into a 1830 x 610 x 100 module for a possible P87 (HO) shunting layout.It might be a close run thing but I suspect it would be quicker and probably cheaper although the ply would have to be thicker. For the boxed beams, I only use 4mm ply but would probably have to use 10mm if it wasn't "boxed".
Posted

Full Member

Doug - thanks for your input too. As ever, an excellent high quality unit. :thumbs Studying it, I could quite easily rout a groove for the corner braces on my router table but I'm not altogether sure the structure would end up saving me much time over my box girder……………:roll::roll: It would certainly save some expensive ply but, and it's maybe the same with you, here, buying PSE timber is a bit like buying bananas - EU regulations say they ought to be straight but they're usually not !!!
I'm told they air dry the timber here rather than kiln drying - but only down to around 15 or 20% then rip it into the required sections. The stresses (and remaining moisture) come out by the time it reaches the woodyard and, by then, it's pretty useless. The lack of "true" timbers was the main reason I went for the box girder in the first place.
'Petermac
Posted

Full Member
The stresses (and remaining moisture) come out by the time it reaches the woodyard and, by then, it's pretty useless. The lack of "true" timbers was the main reason I went for the box girder in the first place.
Yup, it's hard to find good stuff here, I agree, but I suppose I do have the advantage of being able to rip boards and plane/thickness them by machine. For dimensional stability otherwise, ply is hard to beat.
Doug
'You may share the labours of the great, but you will not share the spoil…' Aesop's Fables
"Beer is proof that God loves us and wants us to be happy" - Benjamin Franklin
In the land of the slap-dash and implausible, mediocrity is king
"Beer is proof that God loves us and wants us to be happy" - Benjamin Franklin
In the land of the slap-dash and implausible, mediocrity is king
Posted

Full Member
I'm with you Puffer. I've used plywood 'egg-crate' construction for the past 30 years and I've never had a baseboard go out of square yet. This gives you the option of having flat-eath areas for stations, MPDs etc but still retains the ability to leave the rest of the layout as 'open plan' with the trackbed raised up on plywood risers screwed to the sides of the egg-crate grid. Forming gadients is a piece of cake by just using gradually increased or decreased riser hights.Hi Guys,
My layout baseboards are 12mm ply built in box form but only single thickness. They have been made for over 5 years now and show no sign of twisting. The box construction is 300mm squares by 100mm deep. This egg box structure is then covered by 12mm thick ply. 50mm x 50mm legs are just bolted to this frame in appropriate places for legs with screw adjustable feet. Each vertical piece has a slot cut into it for the wiring. I have an L shaped layout 2.5Mtrs x 900mm deep and the other leg is 1.6Mtrs long by 700mm deep. They are attached by 12mm bolts and wingnuts together with cabinet makers biscuits for alignment.
Hope this is helpful
Puffer
Last edit: by Chinahand
Regards,
Trevor
Trevor
Posted

Site staff


you can see more modules behind this one - they are about 8 ft long by 2' - 2'6" long - light enough to be carried by one person. Everything is glued.
Ron
NCE DCC ; 00 scale UK outline.
NCE DCC ; 00 scale UK outline.
Posted

Full Member
Obviously built by someone who knows what he's doing Sol. A lot of angles in there …………not sure I'm up to that standard.:hmm
'Petermac
Posted

Site staff

He, until he retired, was a Prosecutor in our Police Force.Obviously built by someone who knows what he's doing Sol. A lot of angles in there …………not sure I'm up to that standard.:hmm
Last edit: by Sol
Ron
NCE DCC ; 00 scale UK outline.
NCE DCC ; 00 scale UK outline.
Posted

Full Member
'Petermac
1 guest and 0 members have just viewed this.