Expo 6v Motor and DCC
Posted
#231490
(In Topic #12671)
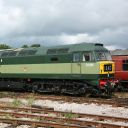
Full Member
Now if this were DC I would have a voltage limiter so no more than 6v would power the motor, would I need the same in DCC so it would be wired something like this MOTOR to DCC chip (programed into NCE cab system,) to voltage limiter to BUS? that looks long wrong to me, or put voltage limiter between motor and chip?
However With this DCC chip having a stand alone address I think I can limit the voltage via the speed CV in the address setup thus doing away with the voltage limiter,
my main concern is not putting more than 6v through the motor as for lining up the tracks I guess by slowing the motor and by eye.
Any thoughts welcome
Mike
Last edit: by cernem1alt
DCC NCE Powercab 00 009 & 009 society member
Posted
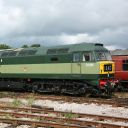
Full Member
DCC Chip wires orange and grey to motor red and black to track then program as you would a loco paying attention to the start, mid and deceleration voltage CVs I set them at 3. The Motor runs smooth not over heating and no need so far for the voltage limiter.
DCC NCE Powercab 00 009 & 009 society member
Posted
Legacy Member
reg
Posted

Full Member
Not so sure about that. Speed in DCC is not done by changing the voltage, it's done by pulse width modulation. As an example using 12v, adjusting the cv values to 50% will give you an average of 6v, it will in reality be 12v for 50% of the time at maximum speed (or whatever voltage your system runs at, mine would be 14.5v, others can be up to 20v). Something you should check. As long as the motor is well ventilated or has a decent heat sink you should be OK. Especially as it will not be run all the time. I would use a voltage limiter between the track and motor, DCC specs call for a minimum of 8 volts, and Digitrax sell a limiter that will reduce the voltage by 3 or 6 volts. You should still be able to control the decoder as normal. Even better use a big 12v motor, which will have a lot more torque (bigger the better, as they rev slower and will not overheat).
Nigel
©Nigel C. Phillips
Posted

Inactive Member
While pulsed 12 Volts may not be overheating the motor, it might be adversely affecting the commutator. Still, if the motor is from the "useful" box it can be swapped out for a 12 Volt one later if problems arise.

Max
Port Elderley
Port Elderley
Posted
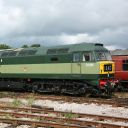
Full Member
Last edit: by cernem1alt
DCC NCE Powercab 00 009 & 009 society member
Posted

Inactive Member
RRampMeter by DCC Specialties | News & Resources
Like I said, if it does any damage, it will only be to the motor and then you can chuck it and get a 12 Volt one.
Max
Port Elderley
Port Elderley
Posted
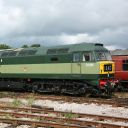
Full Member

DCC NCE Powercab 00 009 & 009 society member
Posted

Site staff

OK what type of power is present at the motor terminals from a decoder?
smoothed DC,
pulsing DC,
what type of meter should be used if it is pulsing DC?
Ron
NCE DCC ; 00 scale UK outline.
NCE DCC ; 00 scale UK outline.
Posted

Inactive Member
The Rramp meter will also work as an accurate Amperes meter with its in line connectors.
I have a couple of them. They are very handy.
Max
Port Elderley
Port Elderley
Posted

Inactive Member
and what answer did you get, Sol?I have asked on a DCC forum this question
OK what type of power is present at the motor terminals from a decoder?
smoothed DC,
pulsing DC,
what type of meter should be used if it is pulsing DC?
Max
Port Elderley
Port Elderley
Posted

Full Member
My understanding (I'm no expert, way too technical for me) is that it's whatever voltage the input from the track is. One role of the decoder is to perform whatever the CVs dictate. Correction to my previous post, and I should have remembered this - decoders use a bridge rectifier to convert the DCC track input to DC output for the EEPROM and then to the motor pulse width modulator, with a voltage drop of about 1.4v though the bridge. So my NCE system with a nominal 14.5v on the track is supplying a constant ~13v DC to the motor. It goes faster or slower depending on what the digital information is telling the CVs to do. That track voltage influences decoder equipped locomotives is seen on track sections with voltage drop - speed drops. Lights and so on just take rectfied DC at whatever the voltage is.
It's a question that has made me wonder at times. I know my LiPo battery dead rail experiments with 11.1v DC input bypassing the bridge rectifier showed that the locomotives ran slightly slower than on regular live track at 14.5v (nominal, closer to 15v in reality).
Mike, that voltage across the motor terminals should be the average voltage. It's still around 12-15v DC depending on the DCC system. NCE should be 15v minus what the the bridge rectifier transistors soak up.You won't see anything like pulses with a digital multimeter, although a sensitive analog one should have the needle twitching. As Max indicated you need a special meter to read the half waveform of DCC current (0 to +14.5 on one rail, 0 to -14.5 on the other)..And an oscilloscope to read DC pulsed outputs.
Small 6v motors are all rpm and low torque (even core-less ones), no substitute for a big 12v motor with low rpm and lots of torque. You didn't say what scale, if this is OO you need all the torque you can get.
Nigel
©Nigel C. Phillips
Posted

Site staff

Pulse width modulated DC.
A multimeter on DC Volts range should read the average voltage, but the very high frequency of the pulses may confuse some meters.
Ron
NCE DCC ; 00 scale UK outline.
NCE DCC ; 00 scale UK outline.
Posted

Full Member
There is a ton of stuff on the net about how a decoder works (most of which is true, which makes a change). Some of it has nice diagrams, which for people like me who want a basic understanding so we don't mess things up, is very useful. It's also useful to plough through the technical specifications for decoders, along with the NMRA standards.
I seem to recall that reducing the pulse width to reduce the speed but still using the original voltage is something you should not do with a coreless motor. Chips tonight is apparently the result as they are not happy handling the excess heat pulses. Hence those voltage reducers for Z scale, which often come with coreless motors for space reasons.
I also recall that open frame motors are better at heat dissipation when using higher than specified voltages than "can" motors, which unless well designed can have poor ventilation. Big cans are usually well ventilated with holes at the ends and have lots of armature mass, which soaks up the heat generated.
The other thing I forgot to mention is that a gearhead motor (which can reduce the rpm to down to 3-5 rpm) but still keep the torque) is ideal for a turntable. That way you can get rid of those gearboxes and have direct drive. Check the current draw before using an OO decoder though.
Hope this helps.
Nigel
©Nigel C. Phillips
Posted

Site staff

Ron
NCE DCC ; 00 scale UK outline.
NCE DCC ; 00 scale UK outline.
Posted

Full Member
The article that Ron linked to is a nice one. The author seems to make the assumption that all DC controllers use voltage-regulated DC. That may have been true back in the day, since the 1980's most controllers include some degree of PWM, if only to smooth out running at low speed settings. Many modern controllers are PWM, with some sophisticated ways of smoothing out sudden jerks in going from zero voltage to full voltage (even the Hornby cheapo has this, although that seems to superimpose constant PWM over changes in voltage). Most PWM controllers used to use a 555 timer, no idea what they use today (just checked, a 555 or similar is still used).
I had a look at that Expo 6v motor. It looks like an older design 3-pole motor, 6500 rpm, used for model robots and similar, with a life of 500 hours according to the manufacturer. Should be OK with intermittent use such as a turntable (even at NCE bus power in fact, 10 seconds a turn?). Your question about putting a voltage limiter between the bus and the motor? (Which I sort of answered previously). If you can put it between the powerpack and the bus I don't see why not as long as it passes through the minimum voltage for DCC operation and getting the digital signal through (8v). The likes of those from Digitrax and MRC (a cheap diode array) are designed to do this. However, you can get a 12v 3.5 rpm geared motor for about double the cost of that Expo 6v motor that would not involve any voltage limiters and should happily accommodate a stationary decoder. I'd use 12v DC and a remote on-off switch if I was doing this, too much messing around to access the accessory decoder numbers even with an NCE system.
Nigel
©Nigel C. Phillips
1 guest and 0 members have just viewed this.