Electrics DCC
Posted
#222289
(In Topic #12124)

Full Member
wiring droppers
Hi All. My soldering is going wrong? The more experience and diligence, the more I make a hash of it.When I returned to model railways it all seemed to be straightforward ? But the more involved I got my work deteriorated. I have been watching YouTube again. Take soldering droppers, please, I purchased a new Iron, fibreglass pen, flux, all the stuff I saw being used to do the job. And I am still melting sleepers( something that I never did before) . Maybe I am using the incorrect size wire? I had some "spare" lighting wire which I stripped off the plastic covering (5 amp type) cut to length stripped and tinned the ends bent the ends as seen on YouTube , threaded the wire through to the buss, then I rubbed the fibreglass pen on the rail to clean it , just to be certain applied some flux, overkill or what? One more thing I purchased off eBay , the bunch of brass in a pot to clean the iron tip, apply the hot iron:oops: another melted sleeper . One idea I saw, the demonstrator avoided using flux, instead he cleaned the track with alcohol and an old toothbrush and placed damp cotton wool each side of the joint to be soldered, to keep it cool.Can anyone help? I am buying more Peco code 75 track than I really require and wasting it with melted sleepers.
''Tis the season to be jolly, Ho Ho Ho Kevin
Staying on the thread Kevin.
Posted

Inactive Member
Let's go step by step. Tell us about your soldering iron.
The tip should be no more than 1 mm diameter, tapering over about 15 mm.
A long, thin tip will allow you to apply the heat neatly between the chairs.
It should be a temperature controlled iron. Mine is set on 35. I'm guessing that's 350 degrees.
Now. Using a small, sharp screwdriver, scrape a small area about 1 mm in diameter on the foot of the rail.
You don't need any special fluxes etc. Plain 60/40 resin core does nicely.
Apply the tip of the iron to the solder and press on to the rail between the ties. Add a bit more solder until there is a blob about 1 mm in diameter melted on to the rail.
If you only allow the very tip of the iron to touch the rail, it will restrict the heat to a tiny area, so not melting the ties.
Once you have your rail blob, strip about 2 mm of the end of the wire and tin the copper core by applying the iron and the solder to it.
If it doesn't tin quickly, you are probably not using copper wire.
Bend the tinned part over in a right angle.
Drill a hole next to the blob of solder on the rail and feed the wire down.
Apply the tip of the iron to the blob and when it melts, pull the wire down until the tinned part enters the blob and its solder melts.
Immediately remove the iron.
The main rule is not to hold the iron on the rail for more than a second or so. Keep pressing and releasing.
Practice.
Max
Port Elderley
Port Elderley
Posted

Full Member
Likewise the wire ends are bent at right angles(another YouTube tip) and there is usually enough solder where I tinned the wire to do the job, even though I don't hold the iron against the rail for long, I still on occasion melt a sleeper. As for the wire it looks like copper. all the best. Kevin
Staying on the thread Kevin.
Posted

Full Member
Max gives good advice and to make sure you stop melting sleepers, simply cut out the plastic web joiner on both rails between the sleepers either side of the solder joint, then slide the two sleepers out of the way before you solder and then slide them back again afterwards. Job done.
Good luck and happy soldering,
Bill
At 6'4'', Bill is a tall chap, then again, when horizontal he is rather long and people often used to trip over him! . . . and so a nickname was born :)
Posted

Inactive Member
A tip of 1/8" is too big. It should be more like 1/16"
Think of an ordinary lead pencil ready for re-sharpening, but with a longer taper.''
A fibreglass pen is a health hazard and cleans too big an area, thus allowing the solder blob to spread too far.
A metal tool will clean only an area of about 1/16" diameter.
Liquid flux is overkill. It makes a mess and runs too far, thus encouraging the solder to do likewise - spreading the heated area.
Bill's idea of pulling back the ties is a good one, but you need to learn to be able to solder in tight places as well.
If I remember the rest, I'll post again.

Max
Port Elderley
Port Elderley
Posted
Inactive Member
I would go along with Max on this . Using flux is a risk , because it
can cause corrosion later on down the Track .

I would also recommend you make the dropper longer than needed
at present , To allow for the fitting of block detectors if and when
you need them . There is nothing more annoying than having to replace
or lengthen the wires to fit detectors later on .
Regards Ted
Posted

Full Member
Staying on the thread Kevin.
Posted

Full Member
Staying on the thread Kevin.
Posted

Full Member
Block Detectors, that is a new one to me, please tell me more, What are they and What do they do?
all the best. Kevin
Staying on the thread Kevin.
Posted
Inactive Member
The only thing I would add is use genuine Lead / tin solder if you can get it. I find it much better than the lead substitute versions and we don't use enough of it to poison ourselves unless we eat it.
I was lucky and got half a dozen rolls or 60/40 in various sizes from the company when the Elf and Safety bod cleared the factory of the full fat leaded. So I haven't tried to obtain it lately.
Now I've finally started a model railway…I've inherited another…
Posted

Inactive Member
Max
Port Elderley
Port Elderley
Posted
Inactive Member
https://www.youtube.com/channel/UC8z5SHQhi9veBOAaFPZffNA/feed
I am sorry to confuse the issue
Block control is used , to allow a computer to be able to track the position of one or
more of your trains as they progress around the track. The computer can then operate
points, signals , turntables or any other operation at the correct time .
If you are considering computer control in the future , then it is worth laying in the ground work now.
The above link will not work directly , but if you type it into google , it will work
Regards Ted
Posted

Full Member
Staying on the thread Kevin.
Posted

Inactive Member
All done with one click of the mouse. (After months of programming.

Max
Port Elderley
Port Elderley
Posted

Full Member
Staying on the thread Kevin.
Posted
Inactive Member
Now I've finally started a model railway…I've inherited another…
Posted

Full Member
Staying on the thread Kevin.
Posted
Inactive Member
http://www.homes24.co.uk/for-sale/details/41725173?search_identifier=246bffe81ed8ef4f01b2161114799bdb#64Q6Gj605gjFclYV.97
I wonder why I moved up here…
sorry it doesn't help you though…
Now I've finally started a model railway…I've inherited another…
Posted
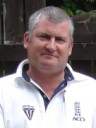
Full Member
All good advice above, I too had the same problem to begin with and I solder at work on a regular basis. I would definitely not use flux on such a small joint.
The way that worked for me was to first file between the sleepers with a small diamond file to rough up the area, I then tinned my dropper but then also angled the dropper to allow a small amount of solder to form a small blob on the dropper. I then held the dropper to the rough area I created with the file and touched the blob of solder with the iron for a split second. I found that doing it that way minimised the contact time of the soldering iron to the track to just a split second.
Each to their own but that's what worked for me.
Shaun
Posted

Full Member
Staying on the thread Kevin.
1 guest and 0 members have just viewed this.